Discover What is Porosity in Welding and Its Result on Architectural Integrity
Discover What is Porosity in Welding and Its Result on Architectural Integrity
Blog Article
Unwinding the Mystery of Porosity in Welding: Tips for Decreasing Defects and Making The Most Of Quality
In the detailed world of welding, porosity continues to be a persistent difficulty that can significantly influence the top quality and integrity of welded joints. Understanding the aspects that add to porosity formation is important in the pursuit of perfect welds. By unraveling the mystery of porosity and implementing reliable strategies for flaw minimization, welders can boost the criteria of their work to attain exceptional top quality results. As we explore the midsts of porosity in welding, uncovering the tricks to its prevention and control will certainly be extremely important for professionals seeking to grasp the art of premium weldments.
Understanding Porosity in Welding
Porosity in welding, a typical problem experienced by welders, refers to the presence of gas pockets or gaps in the bonded product, which can jeopardize the integrity and top quality of the weld. These gas pockets are commonly entraped throughout the welding process due to numerous aspects such as incorrect shielding gas, infected base materials, or inaccurate welding parameters. The development of porosity can deteriorate the weld, making it prone to fracturing and deterioration, inevitably causing architectural failings.
Understanding the source of porosity is important for welders to effectively avoid its event. By identifying the relevance of maintaining correct gas securing, guaranteeing the cleanliness of base materials, and maximizing welding setups, welders can considerably reduce the likelihood of porosity development. Furthermore, utilizing strategies like preheating the base product, using appropriate welding strategies, and carrying out detailed examinations post-welding can even more assist in lessening porosity defects. Generally, an extensive understanding of porosity in welding is crucial for welders to generate top quality and durable welds.

Common Root Causes Of Porosity
When inspecting welding processes for potential top quality concerns, recognizing the usual reasons of porosity is necessary for keeping weld honesty and stopping structural failures. Porosity, characterized by the visibility of dental caries or spaces in the weld metal, can considerably compromise the mechanical residential or commercial properties of a welded joint.
Another widespread reason for porosity is the presence of moisture and impurities on the surface area of the base metal or filler material. When welding products are not effectively cleansed or are subjected to high levels of moisture, the vaporization of these contaminants during welding can produce voids within the weld grain. Additionally, welding at incorrect parameters, such as excessively high travel rates or currents, can create excessive turbulence in the weld pool, capturing gases and triggering porosity. By dealing with these common causes via appropriate gas shielding, product preparation, and adherence to optimum welding specifications, welders can minimize porosity and improve the quality of their welds.
Strategies for Porosity Prevention
Applying effective safety nets is vital in minimizing the incident of porosity in welding processes. One method for porosity avoidance is ensuring appropriate cleansing of the base steel prior to welding. Contaminants such as oil, grease, corrosion, and paint can bring about porosity, so complete cleansing using suitable solvents or mechanical methods is vital.

One more key preventative measure is the choice of the appropriate welding consumables. Utilizing top quality filler products and securing gases that are ideal for the base steel and welding process can considerably minimize the threat of porosity. In addition, keeping correct welding criteria, such as voltage, current, take a trip rate, and gas flow price, is crucial for porosity avoidance. Drifting from the advised setups can lead to incorrect gas protection and insufficient combination, bring about porosity.
In addition, utilizing correct welding techniques, such as preserving a constant travel rate, electrode angle, and arc size, can help stop porosity (What is Porosity). Appropriate training of welders to ensure they comply with best practices and quality assurance procedures is also crucial in reducing porosity problems in welding

Best Practices for High Quality Welds
One trick practice is preserving correct tidiness in the welding location. Thoroughly cleaning up the work wikipedia reference surface and surrounding location prior to welding can help alleviate these concerns.
Another finest technique is to thoroughly pick the appropriate welding specifications for the details materials being joined. This consists of establishing the appropriate voltage, existing, take a trip speed, and protecting gas circulation price. Correct specification option ensures ideal weld infiltration, blend, and total quality. Moreover, using high-grade welding consumables, such as electrodes and filler metals, can considerably impact the final weld high quality. Purchasing costs consumables can cause more powerful, more resilient welds with fewer problems. By complying with these finest methods, welders can continually generate high-grade welds that fulfill sector criteria and go beyond consumer assumptions.
Relevance of Porosity Control
Porosity control plays a crucial duty in making certain the stability and quality of welding joints. Porosity, characterized by the existence of Full Article tooth cavities or voids within the weld steel, can substantially jeopardize the mechanical residential properties and structural honesty of the weld. Extreme porosity compromises the weld, making it extra prone to fracturing, rust, and total failure under functional tons.
Reliable porosity control is necessary for keeping the wanted mechanical properties, such as stamina, ductility, and sturdiness, of the welded joint. What is Porosity. By lessening porosity, welders can enhance the overall high quality and integrity of the weld, guaranteeing that it fulfills the efficiency requirements of the designated application
In addition, porosity control is vital for accomplishing the wanted visual appearance of the weld. Extreme porosity not just damages the weld however likewise diminishes its aesthetic appeal, which can be vital in sectors where visual appeals are essential. Correct porosity control techniques, such as using the appropriate protecting gas, regulating the welding criteria, and guaranteeing proper cleanliness of the base materials, are vital for producing high-grade welds with minimal issues.
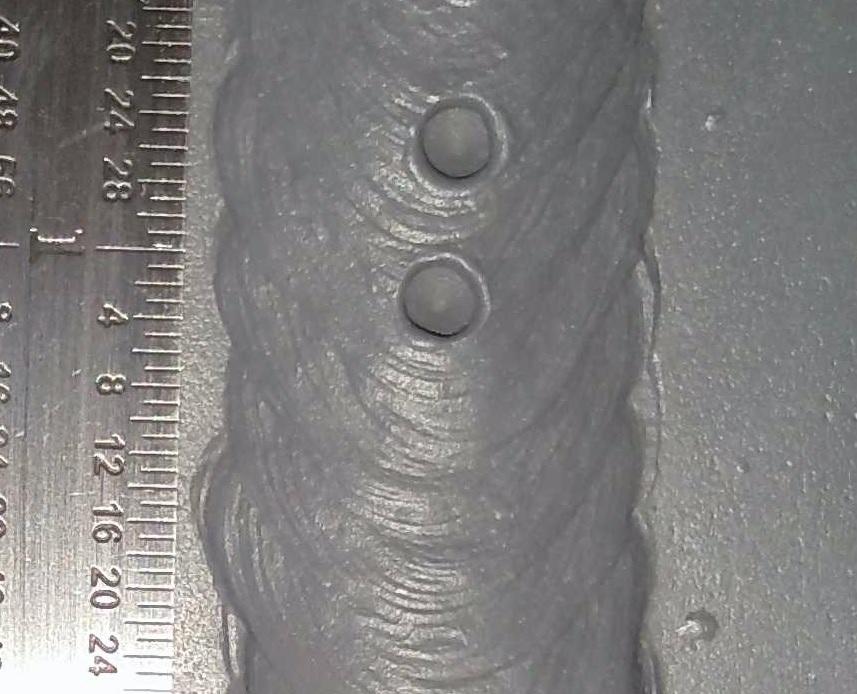
Conclusion
To conclude, porosity in welding is a typical issue that can endanger the high quality of the weld. By understanding the reasons of porosity and carrying out correct avoidance strategies, welders can decrease issues and attain greater top quality welds. It is crucial to manage porosity in welding to make certain the honesty and stamina of the last product. Executing finest practices for visit this site porosity control is essential for achieving optimal welding outcomes.
Report this page